Ultimate Guide to Waterproof Sealants for Electronics: Key Properties and Applications
1. Introduction to Electronics Waterproofing
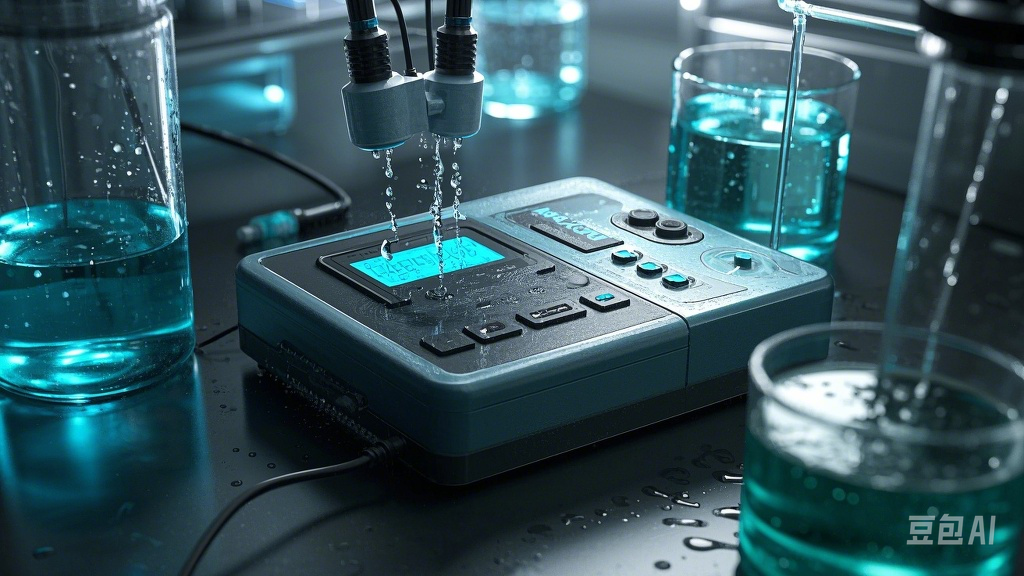
Electronics Waterproofing
In an era of smart devices and IoT technology, waterproofing has become a critical factor in ensuring the reliability and longevity of electronic products. Waterproof sealants play a pivotal role in protecting sensitive components from moisture, dust, and environmental damage. This guide explores the essential features and applications of advanced sealants designed specifically for electronics.
With the ever – increasing integration of technology into our daily lives, electronic devices are no longer just used indoors under ideal conditions. They accompany us during outdoor adventures, in the rain, near water bodies, and in high – humidity environments. For example, a smartphone might get splashed while you’re taking a picture at the beach, or a smartwatch could be exposed to sweat during intense workouts. Even in industrial settings, electronic control panels may face water vapor, condensation, or accidental water contact. Without proper waterproofing, these situations can lead to short – circuits, corrosion of components, and ultimately, device failure.
Waterproof sealants act as a reliable barrier, creating a hermetic or semi – hermetic seal around electronic components. They prevent water molecules from infiltrating the internal circuitry, which is crucial as water can conduct electricity and cause electrical malfunctions. Additionally, by keeping out dust and small particles, sealants also reduce the risk of abrasive damage to moving parts or the accumulation of debris that could interfere with electrical connections.
2. Types of Waterproof Sealants for Electronics
2.2 Silicone Sealants
Silicone sealants are valued for their wide temperature resistance range (-60°C to +200°C) and excellent flexibility. They cure at room temperature, forming a durable, elastic barrier that withstands vibrations and extreme weather conditions. Their chemical inertness ensures compatibility with metals, plastics, and PCBs.
For example, in smart home devices like outdoor security cameras, silicone sealants are often used. These cameras are exposed to various weather conditions throughout the year, from the heat of summer to the cold of winter, and from heavy rain to intense sunlight. The silicone sealant’s ability to maintain its elasticity and adhesion over this wide temperature range ensures that the camera’s housing remains effectively sealed. It prevents water, dust, and insects from entering the camera, which could otherwise damage the sensitive electronic components inside, such as the image sensor, circuit boards, and lenses.
In addition, the chemical inertness of silicone sealants is crucial in preventing any chemical reactions with the materials of the electronic device. This is especially important when dealing with different types of plastics used in electronic enclosures. Some plastics may be sensitive to certain chemicals, and if a sealant reacts with them, it could lead to degradation of the plastic, loss of adhesion, and ultimately, a compromised waterproof seal. Silicone sealants avoid such issues, providing a reliable and long – lasting seal for electronic products.
3. Key Advantages of High-Performance Sealants
3.1 Non-Reactivity and Material Compatibility
Premium sealants are formulated to be chemically inert and non-reactive with electronic components, preventing degradation of PCBs, metals, or coatings. They adhere securely to plastics, glass, and composites without the need for primers. For instance, in the production of smart wearables, where space is limited and components are closely packed, a non – reactive sealant ensures that no chemical reactions occur between the sealant and the delicate electronic parts. This is crucial as any such reaction could lead to a breakdown in the functionality of the device. The strong adhesion to various materials also means that the sealant can effectively seal different types of enclosures, whether they are made of plastic, like in most consumer electronics, or glass, such as in some high – end display devices.
3.2 Long-Term Aging Resistance
Sealants with stable chemical structures and cross – linked polymer structures resist yellowing, cracking, and embrittlement over time. For example, butyl rubber sealants maintain flexibility even after decades of exposure to sunlight and temperature fluctuations. In outdoor electronic equipment like solar panels, which are constantly exposed to the sun’s ultraviolet rays, high – temperature days, and cold nights, the long – term aging resistance of the sealant is of utmost importance. A sealant that can withstand these environmental factors without deteriorating ensures that the solar panel remains waterproof and dustproof throughout its lifespan. This not only protects the internal electronic components but also extends the overall service life of the solar panel, reducing the need for frequent replacements and maintenance.
3.3 IP68/IP69K Compliance
Many modern sealants achieve IP68/IP69K ratings, ensuring protection against submersion and high – pressure water jets. This is critical for devices used in marine, automotive, or outdoor environments. Take smartphones with IP68 – rated sealants as an example. These devices can be safely submerged in water up to a certain depth for a specified period without water ingress. In the automotive industry, sensors and control units often need to withstand high – pressure water jets during car washes or in wet driving conditions. Sealants that meet IP69K standards provide the necessary protection, ensuring the reliable operation of these components even in such harsh environments.
4. Applications in Electronics Manufacturing
4.1 Consumer Electronics
In the realm of consumer electronics, waterproof sealants are everywhere. Take smartphones as an example. The speakers, microphones, and charging ports are highly vulnerable to water damage. Sealants are carefully applied around these components to form a waterproof barrier. When you accidentally drop your phone in a puddle, the sealant around the charging port prevents water from seeping in and short – circuiting the charging circuitry.
Silicone – based sealants are commonly used around LCD panels in tablets. Tablets are often used in various environments, and the silicone sealant between the LCD panel and the device’s frame ensures that moisture does not get trapped between the layers, which could otherwise cause screen discoloration, dead pixels, or complete screen failure. In wearable devices like smartwatches, which are constantly exposed to sweat and potentially splashes of water during daily activities, sealants are used to protect the internal sensors, batteries, and circuit boards. The sealants around the sensors prevent moisture from interfering with the sensor readings, ensuring accurate data collection for features such as heart rate monitoring and step counting.
4.2 Automotive Electronics
Automotive electronics operate in some of the harshest conditions. Engine control units (ECUs) are responsible for managing a vehicle’s engine performance. They are located in the engine bay, which is a high – heat, high – humidity environment with constant exposure to road debris. Sealants are used to protect the delicate electronic components inside the ECU from these elements. A well – sealed ECU can withstand the extreme temperature fluctuations from the engine’s heat during operation to the cold ambient temperatures when the vehicle is parked.
Sensors in cars, such as tire pressure sensors, temperature sensors, and proximity sensors, also rely on sealants. These sensors are often located in exposed areas on the vehicle. For example, tire pressure sensors are installed inside the tires, where they are exposed to moisture, heat, and vibrations. The sealants protect the sensor components from water ingress, which could cause inaccurate readings or sensor failure. In automotive lighting systems, like headlights and taillights, sealants prevent water from entering the housing. Water inside the lights can cause fogging, which reduces visibility and can also damage the bulbs and electrical components. Polyurethane sealants are frequently used in automotive wiring harnesses. These harnesses are subject to vibrations as the vehicle moves, and the polyurethane sealant’s durability and vibration – resistance properties ensure that the electrical connections remain intact over time.
4.3 Industrial Equipment
Industrial equipment, such as industrial controllers used in factories, often operates in environments filled with dust, chemicals, and extreme temperatures. Sealants play a crucial role in protecting the internal electronics of these controllers. For instance, in a manufacturing plant where there is a lot of dust in the air, a sealant – protected industrial controller can continue to function properly without the risk of dust particles interfering with the electrical components, which could lead to malfunctions or system failures.
Industrial cameras used for monitoring production lines or in outdoor industrial applications need to be protected from water, dust, and temperature variations. Sealants are applied to the camera housing to ensure that the lens, image sensor, and other internal components remain in optimal working condition. Motors in industrial equipment also benefit from sealants. These motors may be exposed to chemicals in the industrial environment, and the sealants prevent the chemicals from corroding the motor’s electrical windings and other components. Butyl rubber sealants are favored in dynamic mechanical systems because they can maintain their adhesion even when the components are in constant motion. In conveyor systems, for example, where there are moving parts and vibrations, butyl rubber sealants can keep the electrical enclosures sealed, protecting the control electronics inside.
5. Technical Specifications and Testing
To ensure the effectiveness of waterproof sealants in electronics, they undergo rigorous testing and have well – defined technical specifications. Here are some key aspects:
5.1 Adhesion Strength
Adhesion strength is measured in MPa (megapascals). Different types of sealants have varying adhesion capabilities. Butyl rubber sealants typically offer an adhesion strength in the range of 1.5 – 2.5 MPa. This level of adhesion allows them to firmly bond to various surfaces in electronic devices, such as metal casings or plastic enclosures. For example, in a laptop’s internal components, butyl rubber sealant can securely attach small circuit boards to the metal frame, providing a stable connection while also ensuring waterproofing.
Silicone sealants have an adhesion strength of 1.0 – 1.5 MPa. Although it may seem lower than butyl rubber in terms of numbers, their adhesion is optimized for a wide range of materials, especially plastics and glass. In a smart TV, silicone sealant is used to bond the glass screen to the plastic bezel. Despite the relatively lower adhesion strength value, it can create a reliable seal due to its excellent compatibility with these materials.
Polyurethane sealants, on the other hand, have a higher adhesion strength, ranging from 3.0 – 5.0 MPa. This makes them suitable for applications where a very strong bond is required. In automotive electronics, when sealing the connection between a metal – cased sensor and the vehicle’s body, polyurethane sealant can provide a robust bond that can withstand vibrations and mechanical stress during vehicle operation.
5.2 Elongation at Break
Elongation at break is expressed as a percentage and indicates how much a sealant can stretch before it breaks. Butyl rubber sealants have a high elongation at break, typically 400 – 600%. This high flexibility allows them to adapt to the movement and expansion/contraction of electronic components due to temperature changes. In a handheld game console, which may experience thermal expansion during extended use, the butyl rubber sealant around the battery compartment can stretch and contract without breaking, maintaining the waterproof seal.
Silicone sealants have an elongation at break of 150 – 300%. Their flexibility is still sufficient to handle the normal thermal and mechanical stresses in most electronic devices. In a desktop computer’s power supply unit, the silicone sealant used to seal the connections can tolerate the small movements and temperature – induced expansions/contractions within the unit.
Polyurethane sealants have an elongation at break of 200 – 400%. They offer a good balance between adhesion strength and flexibility. In industrial control panels, where components may be subject to vibrations and temperature fluctuations, polyurethane sealant can maintain its integrity while providing a strong bond to the panel’s housing and internal components.
5.3 Temperature Resistance
The temperature resistance of sealants is crucial as electronic devices can operate in a wide range of temperatures. Butyl rubber sealants can withstand temperatures from – 40°C to +90°C. In cold – storage applications where electronic monitoring devices are used, butyl rubber sealant can ensure the waterproofing of the device even at low temperatures. At the upper end, in some industrial environments with moderate heat, it can also maintain its properties.
Silicone sealants have an extremely wide temperature resistance range, from – 60°C to +200°C. This makes them ideal for applications in aerospace electronics, where components may experience extreme cold during high – altitude flights and intense heat during re – entry. In satellites, silicone sealants are used to protect electronic components from the harsh temperature variations in space.
Polyurethane sealants can resist temperatures from – 50°C to +120°C. In automotive engines, where the temperature can vary greatly depending on the operating conditions, polyurethane sealants are used to protect engine – related electronics. For example, they can seal the connectors of the engine’s fuel injection system, which need to function properly in both cold – start situations and during high – temperature engine operation.
5.4 Water Resistance and Moisture Permeability
All three types of sealants – butyl rubber, silicone, and polyurethane – have excellent water – resistance properties. However, moisture permeability is also an important factor to consider. Moisture permeability is measured in units such as g/m²/day (grams per square meter per day). Lower values indicate better moisture – barrier performance.
Butyl rubber sealants have excellent water resistance and very low moisture permeability. This makes them highly effective in preventing water vapor from reaching sensitive electronic components. In marine electronics, such as underwater cameras, butyl rubber sealants are used to ensure that no moisture can penetrate the device, even when it is submerged in water for long periods.
Silicone sealants also have excellent water resistance and low moisture permeability. Their ability to repel water and prevent moisture ingress is well – known. In outdoor – mounted Wi – Fi routers, silicone sealants are used to protect the internal circuit boards from rain, humidity, and condensation.
Polyurethane sealants have good water resistance, although their moisture permeability may be slightly higher than that of butyl rubber and silicone in some cases. However, they are still suitable for many applications where water resistance is required. In some industrial sensors used in humid environments, polyurethane sealants can provide adequate protection against water and moisture, ensuring the sensor’s accurate operation.
6. Application Best Practices
6.1 Surface Preparation
Before applying the waterproof sealant, surface preparation is crucial. Clean the surfaces thoroughly with isopropyl alcohol. This helps to remove any oils, dust, and moisture that may be present on the surface. Oils can prevent the sealant from adhering properly, while dust can create gaps in the seal, and moisture can interfere with the curing process. For example, in the production of a tablet, the edges of the plastic housing and the areas around the ports must be carefully cleaned with isopropyl alcohol. Any leftover manufacturing residues, such as oils from the injection – molding process or dust from the production environment, can cause the sealant to fail. By ensuring a clean surface, the sealant can form a strong and reliable bond.
6.2 Application Methods
For precise application, automated dispensers are highly recommended. These dispensers can accurately control the amount of sealant dispensed and ensure the formation of a uniform bead. In the production of smartphones, automated dispensers are used to apply the sealant around the charging ports, speakers, and microphones. This precision application ensures that the sealant provides an effective waterproof barrier without excessive use of the sealant, which could potentially affect the device’s aesthetics or functionality. The automated dispensers can be programmed to apply the sealant in specific patterns and thicknesses, depending on the design requirements of the electronic device.
6.3 Curing Conditions
The curing process of the sealant is also important. In a controlled environment with a temperature of 23°C and 50% humidity, allow 24 – 48 hours for the sealant to fully cure. This controlled environment is necessary because temperature and humidity can significantly affect the curing speed and quality of the sealant. For instance, in a high – humidity environment, the sealant may take longer to cure, and there is a risk of moisture being trapped within the sealant, which could lead to long – term degradation of the seal. In a low – temperature environment, the curing process may slow down or even stop, resulting in an incomplete seal. By providing the optimal curing conditions, the sealant can achieve its maximum strength and durability.
6.4 Quality Control
Conducting pressure tests is an essential part of quality control. One common method is to perform a submersion test in water. For example, after applying the sealant to a smartwatch, submerge it in water at a specified depth for a certain period. If the seal is intact, no water should enter the device. Another type of pressure test could involve subjecting the sealed electronic component to air pressure changes. By monitoring the pressure levels and looking for any signs of leakage, manufacturers can ensure that the sealant has formed an effective barrier. Regular quality control checks help to identify any potential issues with the sealant application or the sealant itself, ensuring that only high – quality, waterproof – sealed electronic products reach the market.
7. Future Trends in Sealant Technology
As electronics continue to evolve towards smaller, more integrated designs, the demands on waterproof sealants are becoming increasingly stringent. To meet these challenges, the following trends are emerging in sealant technology:
7.1 Thinner Profiles for Compact Devices
With the miniaturization of electronic devices, there is a growing need for sealants that can form thinner yet highly effective seals. This is crucial for applications such as foldable smartphones and ultra – thin wearable devices. Manufacturers are developing new sealant chemistries that can achieve the same level of water – resistance and adhesion in a much thinner profile. For example, some new silicone – based sealants are being designed to be half the thickness of traditional ones while still maintaining their IP – rated protection. These thinner sealants not only save space within the device but also contribute to the overall sleek and lightweight design that consumers desire.
7.2 Rapid – curing Formulations for High – volume Production
In high – volume electronics manufacturing, time is of the essence. To increase production efficiency, rapid – curing sealants are being developed. These sealants can cure in a matter of minutes or even seconds, compared to the hours or days required by traditional sealants. One approach is the use of ultraviolet (UV) – curable sealants. When exposed to UV light, these sealants can quickly polymerize and form a strong, waterproof seal. This allows for faster assembly lines in the production of consumer electronics like smartphones, tablets, and laptops. In addition, the development of dual – curing sealants, which can cure through both heat and chemical reactions, is also gaining traction. These offer more flexibility in the manufacturing process and can further speed up production times.
7.3 Eco – friendly Materials Compliant with RoHS and REACH Standards
In response to growing environmental concerns, there is a strong push towards the use of eco – friendly sealants. These sealants are made from materials that are compliant with regulations such as RoHS (Restriction of Hazardous Substances) and REACH (Registration, Evaluation, Authorization and Restriction of Chemicals). They contain fewer or no harmful substances like lead, mercury, and certain phthalates. For example, some new bio – based sealants are being developed using renewable raw materials such as plant – derived polymers. These not only reduce the environmental impact of the manufacturing process but also ensure that the end – of – life disposal of electronic products is more environmentally friendly. As consumers become more environmentally conscious, the demand for electronics with eco – friendly sealants is expected to rise, driving further innovation in this area.
8. Conclusion
Choosing the right waterproof sealant is crucial for ensuring the performance and longevity of electronic devices. By prioritizing factors like aging resistance, material compatibility, and application efficiency, manufacturers can deliver products that thrive in challenging environments. Always consult technical datasheets and conduct compatibility tests before mass production to guarantee optimal results. As the electronics industry continues to innovate, the development of advanced sealants will play an increasingly vital role in enabling the next generation of waterproof, reliable devices. Whether it’s the pursuit of thinner profiles, faster – curing times, or more eco – friendly materials, the future of waterproof sealants for electronics holds great promise for enhancing the functionality and durability of our electronic gadgets.
东莞九天量子科技有限公司的密封胶在欧洲市场密封效果表现良好
Dongguan Ninth Quantum Technology Co., Ltd.’s Sealants Excel in European Markets in Sealing Performance
Dongguan Ninth Quantum Technology Co., Ltd. has made a remarkable mark in the European electronics market with its high – performance waterproof sealants. The company’s sealants have been widely adopted in various European – made electronic products, from consumer electronics to industrial equipment.
In the European consumer electronics market, many well – known brands have integrated Dongguan Ninth Quantum Technology’s sealants into their products. For example, a leading European smartphone brand has been using the company’s silicone – based sealants around the charging ports, speakers, and camera modules of its smartphones. These sealants have not only met the strict IP68 waterproof standards but have also demonstrated excellent long – term performance. After months of usage in different European climates, from the rainy weather in the United Kingdom to the humid summers in southern Europe, the sealants have maintained their integrity, preventing water ingress and ensuring the reliable operation of the smartphones.
In the automotive electronics sector in Europe, Dongguan Ninth Quantum Technology’s sealants have also found a niche. German automotive manufacturers, renowned for their high – quality and reliable vehicles, have started using the company’s polyurethane sealants in their engine control units and sensors. These sealants can withstand the high – temperature and high – vibration environment within the engine bay. In the Alps region, where cars need to endure extreme temperature changes during uphill and downhill drives, the sealants in the automotive electronics have proven to be highly effective. They have protected the sensitive components from water, dust, and the mechanical stress caused by the uneven terrain, ensuring the smooth operation of the vehicle’s electronic systems.
For industrial equipment in Europe, especially in the manufacturing hubs of Italy and France, Dongguan Ninth Quantum Technology’s butyl rubber sealants have been well – received. In industrial robots and automated machinery, these sealants are used to protect the control panels and electrical connections. In a busy Italian textile factory, where the environment is filled with dust and humidity, the sealants have kept the industrial electronics free from dust and moisture, reducing the frequency of maintenance and enhancing the overall productivity of the factory.
The success of Dongguan Ninth Quantum Technology Co., Ltd.’s sealants in the European market can be attributed to their excellent sealing performance, strict compliance with international standards, and continuous innovation in product development. As the European electronics market continues to grow and demand higher – quality products, the company is well – positioned to further expand its presence and contribute to the advancement of the electronics waterproofing technology in the region.