Optimization Scheme for the Formulation of High-Performance Wave-Absorbing Silicone Rubber
2025/04/18
0
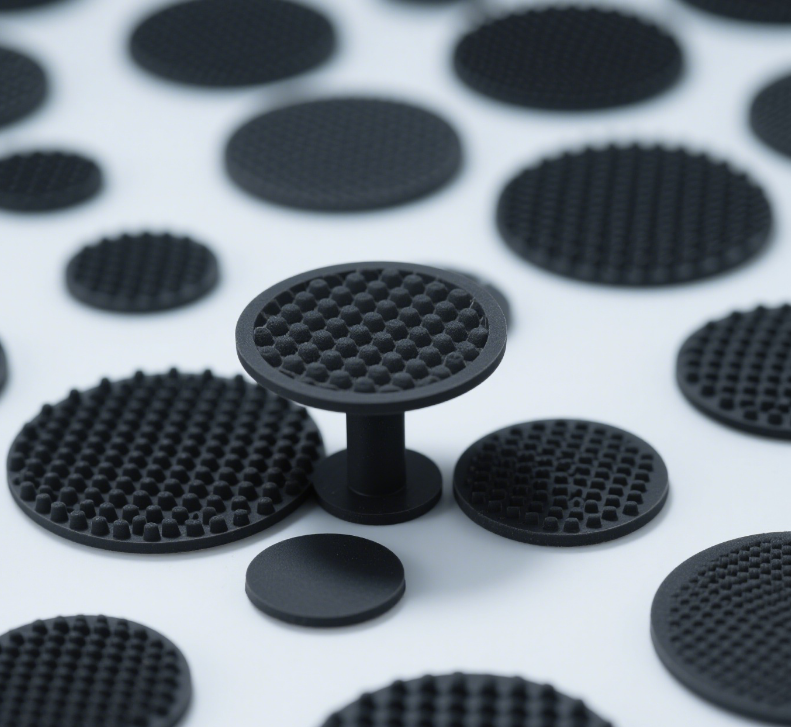
With the rapid development of electronic information technology, the problems of electromagnetic interference (EMI) and electromagnetic radiation have become more and more severe, and the research and development of high-performance wave-absorbing materials is extremely urgent. Silicone rubber has become an ideal matrix for preparing wave-absorbing materials due to its excellent resistance to high and low temperatures, outstanding aging resistance, good flexibility, and excellent processing performance. However, the wave-absorbing ability of the pure silicone rubber matrix is limited, and additives such as wave-absorbing agents need to be added to optimize the formulation to meet the diverse requirements of wave-absorbing performance in different application scenarios. This scheme focuses on comprehensively improving the wave-absorbing performance, mechanical properties, and processing performance of silicone rubber by precisely screening each component and optimizing its proportion.
II. Selection of Raw Materials
(1) Silicone Rubber Matrix
Vinyl silicone rubber is selected as the matrix material. The vinyl content is usually controlled within the range of 0.05% – 0.3%. This content range allows the vinyl silicone rubber to undergo an addition reaction with hydrogen-containing silicone oil under the action of a platinum catalyst, and then vulcanize to form a stable three-dimensional network structure. If the vinyl content is too low, the vulcanization speed will be slow and the cross-linking density will be insufficient; if the content is too high, the hardness of the vulcanized rubber will increase and the flexibility will decrease. Vinyl silicone rubber has the heat resistance to be used for a long time in the temperature range of – 60℃ – 200℃, and its weather resistance and electrical insulation are also very prominent, establishing a solid physical and chemical foundation for the wave-absorbing material.
(2) Wave-Absorbing Agents
. Magnetic Wave-Absorbing Agent: Carbonyl iron powder is used as the magnetic wave-absorbing agent, and its particle size range is set at 5 – 10μm. Carbonyl iron powder can efficiently convert electromagnetic energy into heat energy through hysteresis loss and eddy current loss. The addition amount in the formulation is generally in the range of 15% – 30%. As the addition amount increases, the wave-absorbing performance improves, but excessive addition will significantly damage the mechanical properties of the silicone rubber.
. Electric Loss Type Wave-Absorbing Agent: Carbon nanotubes with a tube diameter of 10 – 30nm and a length of 1 – 10μm are selected as the electric loss type wave-absorbing agent. Carbon nanotubes have excellent electrical conductivity and a large specific surface area, and can form a conductive network in the silicone rubber matrix, absorbing electromagnetic energy through electronic polarization and conductivity loss. The addition amount is controlled within the range of 3% – 8%. Appropriate addition can not only enhance the wave-absorbing performance but also have a certain strengthening effect on the mechanical properties of the silicone rubber.
. Composite Wave-Absorbing Agent: Carbonyl iron powder and carbon nanotubes are compounded according to a mass ratio of 4:1. When the total addition amount of the two reaches 25%, an ideal wave-absorbing effect can be obtained in the X-band (8 – 12GHz), giving full play to the synergistic advantages of magnetic loss and electric loss, broadening the wave-absorbing frequency band, and improving the wave-absorbing intensity.
(3) Vulcanizing Agent and Catalyst
Hydrogen-containing silicone oil with a hydrogen content of 0.1% – 0.3% is selected as the vulcanizing agent. If the hydrogen content is too high, the vulcanization speed will be too fast and bubbles are likely to be generated; if the hydrogen content is too low, the vulcanization reaction will be incomplete. Chloroplatinic acid-isopropanol solution with an addition amount of 0.005% – 0.01% is used as the catalyst. This catalyst can efficiently catalyze the addition reaction between vinyl silicone rubber and hydrogen-containing silicone oil, ensuring the smooth progress of the vulcanization process.
(4) Other Additives
. Reinforcing Filler: Fumed silica with a specific surface area of 200 – 300m²/g is selected as the reinforcing filler, and the addition amount is in the range of 10% – 20%. Fumed silica can form hydrogen bonds with the molecular chains of silicone rubber, significantly increasing the tensile strength, tear strength, and hardness of the silicone rubber, and has little impact on the wave-absorbing performance.
. Plasticizer: Hydroxyl silicone oil with an addition amount of 5% – 10% is used as the plasticizer. Hydroxyl silicone oil can effectively reduce the viscosity of the silicone rubber, improve the processing performance, and at the same time enhance the flexibility and cold resistance of the vulcanized rubber, without having a negative impact on the wave-absorbing performance.
. Coupling Agent: γ-Methacryloxypropyltrimethoxysilane with an addition amount of 1% – 3% is used as the coupling agent. The coupling agent can form chemical bonds on the surface of the fumed silica, enhancing the interfacial bonding force between the fumed silica and the silicone rubber matrix, reducing the agglomeration phenomenon of the filler, and further optimizing the mechanical properties and processing performance of the material.
(1) Silicone Rubber Matrix
Vinyl silicone rubber is selected as the matrix material. The vinyl content is usually controlled within the range of 0.05% – 0.3%. This content range allows the vinyl silicone rubber to undergo an addition reaction with hydrogen-containing silicone oil under the action of a platinum catalyst, and then vulcanize to form a stable three-dimensional network structure. If the vinyl content is too low, the vulcanization speed will be slow and the cross-linking density will be insufficient; if the content is too high, the hardness of the vulcanized rubber will increase and the flexibility will decrease. Vinyl silicone rubber has the heat resistance to be used for a long time in the temperature range of – 60℃ – 200℃, and its weather resistance and electrical insulation are also very prominent, establishing a solid physical and chemical foundation for the wave-absorbing material.
(2) Wave-Absorbing Agents
. Magnetic Wave-Absorbing Agent: Carbonyl iron powder is used as the magnetic wave-absorbing agent, and its particle size range is set at 5 – 10μm. Carbonyl iron powder can efficiently convert electromagnetic energy into heat energy through hysteresis loss and eddy current loss. The addition amount in the formulation is generally in the range of 15% – 30%. As the addition amount increases, the wave-absorbing performance improves, but excessive addition will significantly damage the mechanical properties of the silicone rubber.
. Electric Loss Type Wave-Absorbing Agent: Carbon nanotubes with a tube diameter of 10 – 30nm and a length of 1 – 10μm are selected as the electric loss type wave-absorbing agent. Carbon nanotubes have excellent electrical conductivity and a large specific surface area, and can form a conductive network in the silicone rubber matrix, absorbing electromagnetic energy through electronic polarization and conductivity loss. The addition amount is controlled within the range of 3% – 8%. Appropriate addition can not only enhance the wave-absorbing performance but also have a certain strengthening effect on the mechanical properties of the silicone rubber.
. Composite Wave-Absorbing Agent: Carbonyl iron powder and carbon nanotubes are compounded according to a mass ratio of 4:1. When the total addition amount of the two reaches 25%, an ideal wave-absorbing effect can be obtained in the X-band (8 – 12GHz), giving full play to the synergistic advantages of magnetic loss and electric loss, broadening the wave-absorbing frequency band, and improving the wave-absorbing intensity.
(3) Vulcanizing Agent and Catalyst
Hydrogen-containing silicone oil with a hydrogen content of 0.1% – 0.3% is selected as the vulcanizing agent. If the hydrogen content is too high, the vulcanization speed will be too fast and bubbles are likely to be generated; if the hydrogen content is too low, the vulcanization reaction will be incomplete. Chloroplatinic acid-isopropanol solution with an addition amount of 0.005% – 0.01% is used as the catalyst. This catalyst can efficiently catalyze the addition reaction between vinyl silicone rubber and hydrogen-containing silicone oil, ensuring the smooth progress of the vulcanization process.
(4) Other Additives
. Reinforcing Filler: Fumed silica with a specific surface area of 200 – 300m²/g is selected as the reinforcing filler, and the addition amount is in the range of 10% – 20%. Fumed silica can form hydrogen bonds with the molecular chains of silicone rubber, significantly increasing the tensile strength, tear strength, and hardness of the silicone rubber, and has little impact on the wave-absorbing performance.
. Plasticizer: Hydroxyl silicone oil with an addition amount of 5% – 10% is used as the plasticizer. Hydroxyl silicone oil can effectively reduce the viscosity of the silicone rubber, improve the processing performance, and at the same time enhance the flexibility and cold resistance of the vulcanized rubber, without having a negative impact on the wave-absorbing performance.
. Coupling Agent: γ-Methacryloxypropyltrimethoxysilane with an addition amount of 1% – 3% is used as the coupling agent. The coupling agent can form chemical bonds on the surface of the fumed silica, enhancing the interfacial bonding force between the fumed silica and the silicone rubber matrix, reducing the agglomeration phenomenon of the filler, and further optimizing the mechanical properties and processing performance of the material.
III. Experimental Design for Formulation Optimization
(1) Single-Factor Experiments
. Influence of the Content of Wave-Absorbing Agents on the Wave-Absorbing Performance: Keep the content of other components constant, adjust the content of carbonyl iron powder, carbon nanotubes, and composite wave-absorbing agents respectively, and prepare a series of samples. Use a vector network analyzer to test the reflection loss of the samples in the frequency range of 2 – 18GHz, and draw a reflection loss-frequency curve to determine the optimal addition amount of the wave-absorbing agents.
. Influence of the Content of Reinforcing Fillers on the Mechanical Properties: On the premise of the basic formulation, change the content of fumed silica, and prepare different samples. Test the tensile strength, tear strength, and hardness of the samples, analyze the influence law of the content of fumed silica on the mechanical properties of the silicone rubber, and thus determine its optimal addition amount.
(2) Orthogonal Experiments
Based on the results of the single-factor experiments, select the factors that have a significant impact on the wave-absorbing performance and mechanical properties, such as the content of carbonyl iron powder, the content of carbon nanotubes, the content of fumed silica, and the content of hydrogen-containing silicone oil, and design an orthogonal experiment with four factors and three levels. Through the orthogonal experiment, comprehensively investigate the comprehensive influence of each factor and their interaction on the wave-absorbing performance and mechanical properties of the silicone rubber, and then optimize the formulation combination.
(3) Performance Tests
. Wave-Absorbing Performance Test: Use the arch method to test the reflection loss of the samples in the frequency range of 2 – 18GHz, and set the scanning step size at 0.01GHz. Take the bandwidth with a reflection loss less than -10dB and the maximum reflection loss value as the evaluation indexes of the wave-absorbing performance. The wider the bandwidth and the lower the maximum reflection loss value, the more excellent the wave-absorbing performance.
. Mechanical Performance Test: Test the tensile strength and elongation at break of the samples according to the GB/T 528 – 2009 standard, test the tear strength of the samples according to the GB/T 529 – 2008 standard, and test the hardness of the samples according to the GB/T 531.1 – 2008 standard.
. Processing Performance Test: Evaluate the fluidity, processability, and vulcanization characteristics of the rubber compound by observing the performance of the mixed rubber during the mixing process and the vulcanization process.
(1) Single-Factor Experiments
. Influence of the Content of Wave-Absorbing Agents on the Wave-Absorbing Performance: Keep the content of other components constant, adjust the content of carbonyl iron powder, carbon nanotubes, and composite wave-absorbing agents respectively, and prepare a series of samples. Use a vector network analyzer to test the reflection loss of the samples in the frequency range of 2 – 18GHz, and draw a reflection loss-frequency curve to determine the optimal addition amount of the wave-absorbing agents.
. Influence of the Content of Reinforcing Fillers on the Mechanical Properties: On the premise of the basic formulation, change the content of fumed silica, and prepare different samples. Test the tensile strength, tear strength, and hardness of the samples, analyze the influence law of the content of fumed silica on the mechanical properties of the silicone rubber, and thus determine its optimal addition amount.
(2) Orthogonal Experiments
Based on the results of the single-factor experiments, select the factors that have a significant impact on the wave-absorbing performance and mechanical properties, such as the content of carbonyl iron powder, the content of carbon nanotubes, the content of fumed silica, and the content of hydrogen-containing silicone oil, and design an orthogonal experiment with four factors and three levels. Through the orthogonal experiment, comprehensively investigate the comprehensive influence of each factor and their interaction on the wave-absorbing performance and mechanical properties of the silicone rubber, and then optimize the formulation combination.
(3) Performance Tests
. Wave-Absorbing Performance Test: Use the arch method to test the reflection loss of the samples in the frequency range of 2 – 18GHz, and set the scanning step size at 0.01GHz. Take the bandwidth with a reflection loss less than -10dB and the maximum reflection loss value as the evaluation indexes of the wave-absorbing performance. The wider the bandwidth and the lower the maximum reflection loss value, the more excellent the wave-absorbing performance.
. Mechanical Performance Test: Test the tensile strength and elongation at break of the samples according to the GB/T 528 – 2009 standard, test the tear strength of the samples according to the GB/T 529 – 2008 standard, and test the hardness of the samples according to the GB/T 531.1 – 2008 standard.
. Processing Performance Test: Evaluate the fluidity, processability, and vulcanization characteristics of the rubber compound by observing the performance of the mixed rubber during the mixing process and the vulcanization process.
IV. Experimental Results and Analysis
(1) Results of Single-Factor Experiments
. Influence of the Content of Wave-Absorbing Agents: When the content of carbonyl iron powder exceeds 25%, the reflection loss in the high-frequency band (12 – 18GHz) begins to decrease, and at the same time, the hardness of the material increases significantly. When the content of carbon nanotubes reaches 5%, a better wave-absorbing effect can be obtained in the high-frequency band (10 – 18GHz). Continuing to increase the content has little obvious improvement effect on the wave-absorbing performance and will lead to poor fluidity of the material. Under a specific proportion and addition amount, the composite wave-absorbing agent has a bandwidth with a reflection loss less than -10dB of up to 3.5GHz in the X-band (8 – 12GHz), and the maximum reflection loss is -18dB.
. Influence of the Content of Reinforcing Fillers: As the content of fumed silica increases, the tensile strength, tear strength, and hardness of the silicone rubber gradually increase. When the content reaches 15%, the improvement of mechanical properties tends to be gentle, and continuing to increase the content will lead to a sharp increase in the viscosity of the rubber compound and a deterioration of the processing performance.
(2) Results of Orthogonal Experiments
Through the analysis of the data of the orthogonal experiment, the optimal formulation of high-performance wave-absorbing silicone rubber is determined: 100 parts of vinyl silicone rubber, 20 parts of carbonyl iron powder, 5 parts of carbon nanotubes, 15 parts of fumed silica, 1.5 parts of hydrogen-containing silicone oil, 0.008 parts of chloroplatinic acid-isopropanol solution, 8 parts of hydroxyl silicone oil, and 2 parts of γ-methacryloxypropyltrimethoxysilane. Under this formulation, the silicone rubber has a bandwidth with a reflection loss less than -10dB of 4GHz in the frequency range of 8 – 12GHz, the maximum reflection loss is -20dB, the tensile strength reaches 8MPa, the tear strength is 25kN/m, and the hardness is 55 Shore A, showing excellent comprehensive performance.
(1) Results of Single-Factor Experiments
. Influence of the Content of Wave-Absorbing Agents: When the content of carbonyl iron powder exceeds 25%, the reflection loss in the high-frequency band (12 – 18GHz) begins to decrease, and at the same time, the hardness of the material increases significantly. When the content of carbon nanotubes reaches 5%, a better wave-absorbing effect can be obtained in the high-frequency band (10 – 18GHz). Continuing to increase the content has little obvious improvement effect on the wave-absorbing performance and will lead to poor fluidity of the material. Under a specific proportion and addition amount, the composite wave-absorbing agent has a bandwidth with a reflection loss less than -10dB of up to 3.5GHz in the X-band (8 – 12GHz), and the maximum reflection loss is -18dB.
. Influence of the Content of Reinforcing Fillers: As the content of fumed silica increases, the tensile strength, tear strength, and hardness of the silicone rubber gradually increase. When the content reaches 15%, the improvement of mechanical properties tends to be gentle, and continuing to increase the content will lead to a sharp increase in the viscosity of the rubber compound and a deterioration of the processing performance.
(2) Results of Orthogonal Experiments
Through the analysis of the data of the orthogonal experiment, the optimal formulation of high-performance wave-absorbing silicone rubber is determined: 100 parts of vinyl silicone rubber, 20 parts of carbonyl iron powder, 5 parts of carbon nanotubes, 15 parts of fumed silica, 1.5 parts of hydrogen-containing silicone oil, 0.008 parts of chloroplatinic acid-isopropanol solution, 8 parts of hydroxyl silicone oil, and 2 parts of γ-methacryloxypropyltrimethoxysilane. Under this formulation, the silicone rubber has a bandwidth with a reflection loss less than -10dB of 4GHz in the frequency range of 8 – 12GHz, the maximum reflection loss is -20dB, the tensile strength reaches 8MPa, the tear strength is 25kN/m, and the hardness is 55 Shore A, showing excellent comprehensive performance.
V. Conclusion
Through the reasonable screening of each component and the precise optimization of the proportion, a wave-absorbing silicone rubber material with excellent comprehensive performance has been successfully developed. This optimal formulation can be flexibly adjusted according to the specific requirements of wave-absorbing performance and mechanical properties in different application scenarios, providing a powerful reference basis for the industrial production and practical application of high-performance wave-absorbing silicone rubber materials.
Through the reasonable screening of each component and the precise optimization of the proportion, a wave-absorbing silicone rubber material with excellent comprehensive performance has been successfully developed. This optimal formulation can be flexibly adjusted according to the specific requirements of wave-absorbing performance and mechanical properties in different application scenarios, providing a powerful reference basis for the industrial production and practical application of high-performance wave-absorbing silicone rubber materials.