Processability and Molding Technology of Wave-Absorbing Silicone Rubber
2025/04/18
0
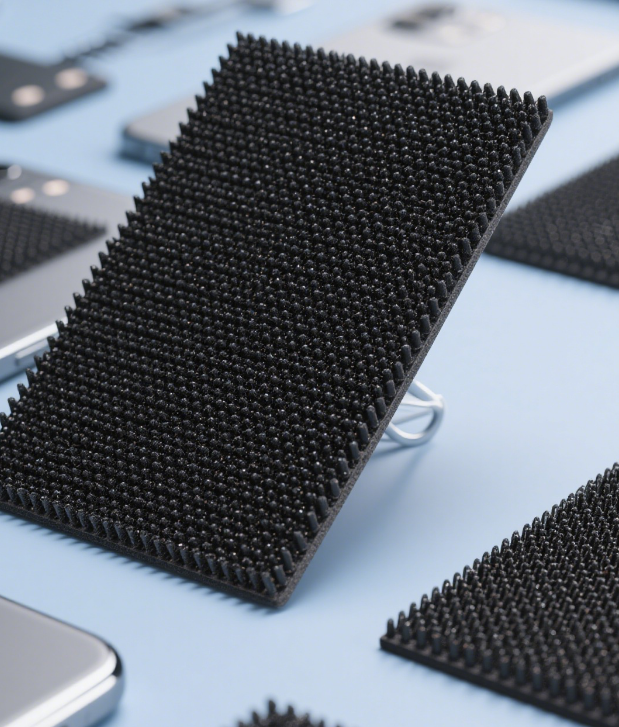
As a material that combines the wave-absorbing function and the excellent properties of silicone rubber, wave-absorbing silicone rubber is widely used in fields such as electronic communication, national defense and military industry, and aerospace. However, the realization of its performance advantages depends on good processability and molding technology. A reasonable processing and molding method can ensure that the wave-absorbing silicone rubber is accurately formed into the required components, while maintaining its wave-absorbing performance and physical and mechanical properties. This article will elaborate in detail on the processability characteristics of wave-absorbing silicone rubber, common molding technologies, factors affecting processability, and future development trends.
II. Processability Characteristics of Wave-Absorbing Silicone Rubber
(1) Good Flexibility and Plasticity
Silicone rubber itself has a unique macromolecular chain structure, and the molecular chain has good flexibility, which endows the wave-absorbing silicone rubber with good flexibility and plasticity. During the processing process, the wave-absorbing silicone rubber can be deformed under a certain external force and adapt to the requirements of different shaped molds, so it can be formed into components with complex shapes, such as stealth materials with curved surface structures and shielding parts of electronic devices with irregular shapes.
(2) Compatibility with Multiple Processing Technologies
Wave-absorbing silicone rubber can be compatible with a variety of traditional rubber processing technologies, such as compression molding, extrusion molding, injection molding, etc. In addition, with the development of technology, it can also be combined with some emerging processing technologies, such as 3D printing molding. This wide range of process compatibility enables wave-absorbing silicone rubber to select the most suitable processing method according to the needs of different products and the production scale.
(3) Controllability of the Impact of the Processing Process on Performance
By reasonably controlling the processing process parameters, such as temperature, pressure, time, etc., the impact of the processing process on the wave-absorbing performance and physical and mechanical properties of the wave-absorbing silicone rubber can be effectively reduced. For example, during the vulcanization process, precisely controlling the vulcanization temperature and time can not only ensure that the silicone rubber is fully cross-linked to form a stable network structure, but also avoid the agglomeration of wave-absorbing fillers or the decline in performance caused by over-vulcanization.
(1) Good Flexibility and Plasticity
Silicone rubber itself has a unique macromolecular chain structure, and the molecular chain has good flexibility, which endows the wave-absorbing silicone rubber with good flexibility and plasticity. During the processing process, the wave-absorbing silicone rubber can be deformed under a certain external force and adapt to the requirements of different shaped molds, so it can be formed into components with complex shapes, such as stealth materials with curved surface structures and shielding parts of electronic devices with irregular shapes.
(2) Compatibility with Multiple Processing Technologies
Wave-absorbing silicone rubber can be compatible with a variety of traditional rubber processing technologies, such as compression molding, extrusion molding, injection molding, etc. In addition, with the development of technology, it can also be combined with some emerging processing technologies, such as 3D printing molding. This wide range of process compatibility enables wave-absorbing silicone rubber to select the most suitable processing method according to the needs of different products and the production scale.
(3) Controllability of the Impact of the Processing Process on Performance
By reasonably controlling the processing process parameters, such as temperature, pressure, time, etc., the impact of the processing process on the wave-absorbing performance and physical and mechanical properties of the wave-absorbing silicone rubber can be effectively reduced. For example, during the vulcanization process, precisely controlling the vulcanization temperature and time can not only ensure that the silicone rubber is fully cross-linked to form a stable network structure, but also avoid the agglomeration of wave-absorbing fillers or the decline in performance caused by over-vulcanization.
III. Common Molding Technologies
(1) Compression Molding
(1) Compression Molding
- Process Principle: Put the mixed wave-absorbing silicone rubber compound into the preheated mold cavity, and vulcanize and form the compound in the mold under a certain temperature and pressure. This process is suitable for the production of wave-absorbing silicone rubber products with relatively complex shapes and high requirements for dimensional accuracy, such as shielding covers of electronic devices and wave-absorbing gaskets.
- Process Key Points: The mold design needs to consider the shape, dimensional accuracy and demoulding requirements of the product; control the compression molding temperature (generally 120 – 180°C), pressure (10 – 30MPa) and time (5 – 30 minutes) well to ensure that the compound is fully vulcanized and the product has no defects such as bubbles and lack of compound; be careful when demoulding to avoid damaging the product.
(2) Extrusion Molding - Process Principle: Use the pressure generated by the rotation of the screw to continuously extrude the wave-absorbing silicone rubber compound from the die orifice, and obtain the products with the required shape through cooling and shaping, such as wave-absorbing sealing strips and cable sheaths. Extrusion molding has the characteristics of high production efficiency and stable product dimensions, and is suitable for continuous production.
- Process Key Points: Select a suitable die according to the shape of the product; control the extrusion temperature (the barrel temperature is generally 60 – 120°C, and the die temperature is slightly higher than the barrel temperature) to ensure that the compound has good fluidity; adjust the screw speed and traction speed to ensure the dimensional accuracy and surface quality of the product; during the cooling and shaping process, reasonably control the cooling speed to prevent the product from deforming.
(3) Injection Molding - Process Principle: Heat and plasticize the wave-absorbing silicone rubber compound through the barrel of the injection molding machine, and then inject it at high speed into the closed mold cavity under the push of the screw. After pressure holding and vulcanization, open the mold and take out the product. Injection molding has high production efficiency, high product dimensional accuracy and good surface quality, and is suitable for mass production of small wave-absorbing silicone rubber products with complex shapes, such as wave-absorbing encapsulation parts of electronic components.
- Process Key Points: Precisely control the injection temperature (the barrel temperature is generally 80 – 140°C, and the mold temperature is generally 100 – 160°C) and injection pressure (50 – 150MPa) to ensure that the compound quickly fills the mold cavity; reasonably set the pressure holding time and cooling time to prevent the product from having defects such as shrinkage cavities and deformation; the mold design needs to consider the gating system and exhaust system to ensure smooth flow of the compound and exhaust of gas.
(4) 3D Printing Molding - Process Principle: Based on the additive manufacturing technology, the wave-absorbing silicone rubber is made into a printing material with good fluidity (such as liquid silicone rubber or silicone rubber filament), and is stacked layer by layer according to the designed 3D model through a 3D printer for molding. 3D printing molding can realize the rapid manufacturing of products with complex structures and personalized customization, opening up a new way for the application of wave-absorbing silicone rubber.
- Process Key Points: Develop wave-absorbing silicone rubber materials suitable for 3D printing, and adjust the properties such as the viscosity and curing speed of the materials; optimize the printing parameters, such as printing temperature, nozzle moving speed, layer thickness, etc., to ensure the stability of the printing process and the accuracy of the product; for the printed products, post-processing (such as secondary vulcanization) may be required to improve the performance.
IV. Factors Affecting Processability
(1) Formulation Composition
(1) Formulation Composition
- Wave-Absorbing Fillers: The type, content and particle size of wave-absorbing fillers have a significant impact on the processability of wave-absorbing silicone rubber. For example, if the content of magnetic fillers (such as carbonyl iron powder) is too high, the viscosity of the compound will increase, the fluidity will become worse, and the processing will be difficult; if the particle size of the filler is too small, it is easy to agglomerate, affecting the dispersibility, and then affecting the processing performance and product quality.
- Additives: The types and dosages of additives such as plasticizers, vulcanizing agents, and accelerators will change the processing performance of wave-absorbing silicone rubber. An appropriate amount of plasticizer can reduce the viscosity of the compound and improve the fluidity; however, excessive use may lead to a slower vulcanization speed and a decline in the mechanical properties of the product. The selection and dosage of vulcanizing agents and accelerators directly affect the vulcanization speed and cross-linking degree, and precise control is required to ensure the smooth progress of the processing process.
(2) Processing Process Parameters - Temperature: If the processing temperature is too high, the silicone rubber will vulcanize or decompose in advance, affecting the product quality; if the temperature is too low, the fluidity of the compound will be poor, and it will be difficult to form. Different molding processes have different temperature requirements, and adjustments need to be made according to the specific process and material characteristics.
- Pressure: In molding processes such as compression molding and injection molding, insufficient pressure will lead to incomplete filling of the compound, and the product will have defects such as lack of compound and air holes; excessive pressure may damage the mold or cause internal stress in the product, affecting the performance.
- Time: Insufficient vulcanization time will result in insufficient cross-linking of the silicone rubber, and the product will have poor mechanical properties and aging resistance; excessive vulcanization time will lead to over-vulcanization of the product, an increase in hardness, a decrease in flexibility, and at the same time, it will also reduce the production efficiency.
(3) Equipment and Molds
The performance of the equipment and the design of the molds are crucial for the processing and molding of wave-absorbing silicone rubber. Advanced processing equipment can more precisely control the process parameters and ensure the processing quality; a reasonable mold design (such as runner design, exhaust design, demoulding design, etc.) helps the flow and molding of the compound and reduces product defects.
V. Strategies for Improving Processability and Molding Technology
(1) Optimizing Formulation Design
(1) Optimizing Formulation Design
- Reasonable Selection of Fillers: Give priority to wave-absorbing fillers with good dispersibility and little impact on the fluidity of the compound, and improve the compatibility between the filler and the silicone rubber matrix through surface modification technologies (such as coupling agent treatment). For example, using carbon nanotubes treated with silane coupling agents can improve their dispersibility in silicone rubber and reduce the negative impact on the processing performance.
- Adjusting the Dosage of Additives: According to the processing process and product performance requirements, precisely adjust the dosages of additives such as plasticizers and vulcanizing agents, and optimize the processing performance of the compound on the premise of ensuring the product performance. For example, using new high-efficiency vulcanizing agents can shorten the vulcanization time and improve the production efficiency.
(2) Improving the Processing Process - Adopting New Processing Technologies: Explore and apply emerging processing technologies, such as micro-injection molding, composite molding technologies that combine hot pressing molding with 3D printing, etc., to meet the requirements of different products for processing accuracy and production efficiency.
- Optimizing Process Parameters: Through experiments and simulation analysis, determine the optimal process parameters of each wave-absorbing silicone rubber material under different molding processes to achieve precise control of the processing process. For example, use computer simulation software to simulate the injection molding process, and optimize parameters such as injection temperature, pressure and time to improve the product quality.
(3) Strengthening the Research and Development of Equipment and Molds
Develop high-precision and automated processing equipment to improve the control accuracy and stability of the equipment for process parameters. At the same time, strengthen the research on mold design and manufacturing technologies, and adopt advanced mold manufacturing processes (such as electrical discharge machining, laser processing, etc.) to improve the accuracy and service life of the molds and ensure the molding quality of wave-absorbing silicone rubber products.
VI. Future Development Trends
(1) Intelligent Processing and Molding
With the development of intelligent manufacturing technology, the processing and molding of wave-absorbing silicone rubber will develop in the direction of intelligence. By introducing sensors, automated control systems and big data analysis technology, real-time monitoring and precise control of the processing process can be realized, and the production efficiency and product quality stability can be improved.
(2) Green Processing Technology
The increasing environmental protection requirements prompt the processing and molding technology of wave-absorbing silicone rubber to develop in the direction of greening. In the future, more environmentally friendly raw materials and processing processes will be developed to reduce energy consumption and waste emissions during the processing process and achieve sustainable development.
(3) Multi-Functional Integrated Molding
To meet the needs of complex application scenarios, the molding technology of wave-absorbing silicone rubber will develop in the direction of multi-functional integration. For example, during the molding process, the integration of wave-absorbing performance with other functions (such as self-healing, heat conduction, conductivity, etc.) can be realized, and composite material products with multiple functions can be developed.
(1) Intelligent Processing and Molding
With the development of intelligent manufacturing technology, the processing and molding of wave-absorbing silicone rubber will develop in the direction of intelligence. By introducing sensors, automated control systems and big data analysis technology, real-time monitoring and precise control of the processing process can be realized, and the production efficiency and product quality stability can be improved.
(2) Green Processing Technology
The increasing environmental protection requirements prompt the processing and molding technology of wave-absorbing silicone rubber to develop in the direction of greening. In the future, more environmentally friendly raw materials and processing processes will be developed to reduce energy consumption and waste emissions during the processing process and achieve sustainable development.
(3) Multi-Functional Integrated Molding
To meet the needs of complex application scenarios, the molding technology of wave-absorbing silicone rubber will develop in the direction of multi-functional integration. For example, during the molding process, the integration of wave-absorbing performance with other functions (such as self-healing, heat conduction, conductivity, etc.) can be realized, and composite material products with multiple functions can be developed.
VII. Conclusion
The processability and molding technology of wave-absorbing silicone rubber are key links for its wide application. Understanding its processability characteristics, mastering common molding technologies, analyzing influencing factors and taking corresponding optimization strategies are of great significance for improving the quality and production efficiency of wave-absorbing silicone rubber products. With the continuous development of technology, the processing and molding technology of wave-absorbing silicone rubber will continue to innovate and improve, providing strong support for its application in more fields.
The processability and molding technology of wave-absorbing silicone rubber are key links for its wide application. Understanding its processability characteristics, mastering common molding technologies, analyzing influencing factors and taking corresponding optimization strategies are of great significance for improving the quality and production efficiency of wave-absorbing silicone rubber products. With the continuous development of technology, the processing and molding technology of wave-absorbing silicone rubber will continue to innovate and improve, providing strong support for its application in more fields.
This report systematically combs the relevant content of the processability and molding technology of wave-absorbing silicone rubber. If you want to know more details about a certain type of molding technology, or have other needs, you are welcome to communicate with me at any time.
请将这段英文翻译成中文。
吸波硅橡胶的常见成型技术有哪些优缺点?
如何提高吸波硅橡胶的可加工性?